دليل اختيار المواد
للتطبيقات الاقتصادية منخفضة الارتفاع
يعد اختيار المادة المناسبة بناءً على سيناريوهات تشغيلية محددة أمرًا بالغ الأهمية للأداء والمتانة.
بالإشارة إلى مصفوفة السيناريو الموضحة في الكتاب الأبيض حول اقتصاد الارتفاع المنخفض الصادر عن الجمعية الصينية للملاحة الجوية والفضائية، فإننا نسلط الضوء علىحلول المواد النموذجية للتطبيقات الرئيسية.
السيناريو 1: العمليات الزراعية والغاباتفي الزراعة والغابات وتربية الحيوانات ومصايد الأسماك، تُستخدم المركبات الجوية على نطاق واسع لنقل المحاصيل والبذر والتفتيش الميداني ورش المبيدات الحشرية وتوصيل زريعة الأسماك ودوريات مكافحة الحرائق.ينبغي أن يعطي اختيار المواد في هذا القطاع الأولوية لما يلي:مقاومة الرطوبة والحرارةمقاومة التآكل الكيميائيتتضمن حلول المواد الموصى بها ما يلي:المكونات الهيكلية الحاملة للحمل الرئيسية(على سبيل المثال، إطارات جسم الطائرة، وأقواس الرش)PA6-GF30قوة عالية ومقاومة ممتازة للتعب. يمكن تقليل امتصاص الرطوبة بالمعالجات السطحية المناسبة. مناسب للعمليات الزراعية طويلة الأمد وذات الأحمال الثقيلة.سبيكة PPO/PSمقاوم للهب والتآكل الناتج عن المبيدات الحشرية. مثالي للأجزاء الدقيقة مثل حوامل خزانات المبيدات الحشرية وأغطية الصمامات.سبائك التيتانيوممتانة استثنائية ومقاومة للتآكل. مثالية للأجزاء المعرضة بشدة للضغط والإجهاد المتكرر، مثل موصلات ذراع الرش.المكونات المكشوفة المقاومة للمواد الكيميائية(على سبيل المثال، فوهات الرش، وخزانات المبيدات الحشرية، وخطوط الأنابيب)PPS-GF40 مع بطانة من سبائك التيتانيوميوفر الجمع بين مقاومة PPS لدرجات الحرارة العالية والمواد الكيميائية مع بطانة التيتانيوم حماية ممتازة ضد اختراق المبيدات الحشرية، مما يطيل عمر المكونات بشكل كبير.مكونات داخلية خفيفة الوزن(على سبيل المثال، لوحات التحكم، وتصميمات قمرة القيادة الداخلية، وألواح البطانة الداخلية)نظام ABSاقتصادي وسهل التشكيل. مناسب للأجزاء الداخلية غير الحاملة للأحمال؛ يُنصح بتجنب التعرض المباشر للمواد الكيميائية.PC (بولي كربونات)مقاومة ممتازة للصدمات، مثالية للأغطية الواقية لشاشات المراقبة أو نوافذ المراقبة.سبائك الألومنيومخفيف الوزن، سهل التشكيل، ومقاوم جدًا للبيئات الرطبة بعد الأكسدة. أكثر اقتصادًا من سبائك التيتانيوم للأجزاء غير الحساسة.
السيناريو 2: تطبيقات النقل
في سيناريوهات النقل، تُستخدم المركبات الجوية في المقام الأول لنقل الركاب والبضائع، والتصوير الجوي، والاستجابة للطوارئ، وخدمات الإنقاذ.
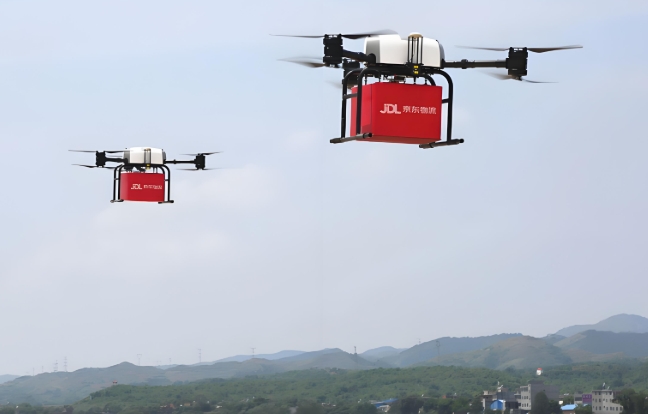
ونظراً لهذه التطبيقات، يجب أن يركز اختيار المواد على:
تصميم خفيف الوزن لتعزيز المرونة والقدرة على التحمل أثناء الطيران
صلابة عالية وقوة لتحمل الضغوط الهيكلية الكبيرة والتأثيرات الخارجية
بناءً على المتطلبات المحددة، فإن حلول المواد الموصى بها هي كما يلي:
الهياكل الحاملة للأحمال الأساسية
(على سبيل المثال، إطارات جسم الطائرة، معدات الهبوط)
PA6-GF30
صلابة عالية وخصائص خفيفة الوزن، مما يحسن كفاءة الحمولة والسلامة التشغيلية.
بيك-سي اف 40
قوة استثنائية ومقاومة للتعب، مناسبة للموصلات الحرجة في أجهزة الإنقاذ في حالات الطوارئ (على سبيل المثال، آليات الرفع).
سبائك التيتانيوم
نسبة قوة إلى وزن ممتازة، مثالية لنقاط الهيكل عالية التحميل وعالية الأمان على طائرات الإنقاذ (على سبيل المثال، واجهات خطاف الإنقاذ).
سبائك الألومنيوم
خفيف الوزن مع قوة عالية نسبيًا، يمكن أن يحل محل PA6-GF30 في الهياكل الحاملة للحمل الثانوي (على سبيل المثال، حوامل حاوية الشحن).
المكونات الداخلية الوظيفية
(على سبيل المثال، لوحات العدادات، والأقواس، ومفصلات أبواب المقصورة، والموصلات)
سبائك PC/ABS
يحقق التوازن بين مقاومة الحرارة وقابلية المعالجة، وهو مناسب للأجزاء الهيكلية ذات الشكل المعقد مع تقليل الوزن والحفاظ على القوة.
سبائك الألومنيوم
قابلية تصنيع فائقة مقارنة بالتيتانيوم، مثالية للمكونات المتحركة بدقة والتي تتطلب تحملات ضيقة.
مكونات متحركة عالية السرعة
(على سبيل المثال، أعمدة الدوار، تروس ناقل الحركة)
PEEK-CF40 مع طلاء سبائك التيتانيوم
ميزة التركيبة: توفر مادة PEEK مقاومة ممتازة للتآكل وتخميد الاهتزازات، بينما تعمل طبقة التيتانيوم على تعزيز صلابة السطح ومقاومة درجات الحرارة العالية.
مكونات المراقبة الشفافة
(على سبيل المثال، النوافذ، وأغطية الكاميرات)
البولي كربونات (PC)
شفاف ومقاوم للصدمات، مما يضمن رؤية واضحة لمعدات التصوير الجوي.
السيناريو 3: مراقبة البيئة البحرية
في البيئات البحرية، تعمل المعدات غالبًا في ظل ظروف رذاذ الملح والرطوبة العالية وتآكل مياه البحر.
لذلك، يجب أن تظهر الموادمقاومة كيميائية ممتازة، وخاصةً ضد رذاذ الملح وتآكل مياه البحر. بالإضافة إلى ذلك، هناك درجة معينة منمقاومة الحرارةيجب أن يتحمل التعرض لأشعة الشمس لفترات طويلة.وبناءً على هذه المتطلبات البيئية، فإن حلول المواد الموصى بها هي كما يلي:المكونات شديدة التعرض(على سبيل المثال، أغلفة المستشعر، والأقواس الخارجية، وحوامل المستشعر، والعوامات)سبائك التيتانيوممقاومة استثنائية للتآكل الناتج عن مياه البحر، مثالية لأغلفة أجهزة الاستشعار أو هياكل التثبيت المغمورة لفترات طويلة.سبائك الألومنيوم المؤكسدمقاومة محسنة لرذاذ الملح بعد معالجة الأكسدة، مناسبة للعوامات الفعالة من حيث التكلفة أو الأقواس الداعمة الخارجية.سبيكة PPO/PSمقاومة ممتازة للتآكل في مياه البحر، ومناسبة لأجهزة المراقبة الدقيقة العاملة في بيئات رذاذ الملح أو الغمر.PPS-GF40مقاومة درجات الحرارة العالية ومقاومة للهب، مثالية للمكونات الموجودة حول حجرات المحرك أو تركيبات الألواح الشمسية.مكونات جهاز المراقبة الأساسية(على سبيل المثال، حاويات البيانات، والأغلفة المختومة)بيك-سي اف 40مقاومة فائقة للزحف وامتصاص منخفض للرطوبة، مما يمنع تدهور الأداء في البيئات ذات الرطوبة العالية؛ مثالي للأدوات الدقيقة ذات العمر الطويل.كابينة محكمة الغلق للأجهزة الدقيقةإطار من سبائك PPO/PS + سبائك التيتانيومميزة الجمع: يوفر سبيكة PPO/PS مقاومة للتآكل الناتج عن مياه البحر، بينما يوفر إطار التيتانيوم صلابة هيكلية لمنع التشوه.المناطق ذات درجات الحرارة المرتفعة(على سبيل المثال، أغلفة المحرك، وقنوات العادم)PPS-GF40 مع مثبتات من سبائك التيتانيومميزة الجمع: توفر مادة PPS مقاومة للحرارة والتآكل، بينما تمنع مثبتات التيتانيوم فشل الاتصال بسبب صدأ المعدن.ملخصالتطبيقات الحساسة للتكلفة (على سبيل المثال، الزراعة والغابات):استخدم بشكل أساسي PA6-GF30 + سبيكة الألومنيوم، مع تطبيق PPS-GF40 أو سبيكة التيتانيوم فقط على المناطق الحرجة المعرضة للتآكل الكيميائي (على سبيل المثال، نقاط التعرض للمبيدات الحشرية).تطبيقات الأداء أولاً (على سبيل المثال، الإنقاذ والنقل):خلط سبائك التيتانيوم مع PEEK-CF40 للهياكل الحاملة للأحمال الأساسية، وتحقيق التوازن بين التصميم خفيف الوزن والقوة الميكانيكية القصوى.تطبيقات البيئات القاسية (على سبيل المثال، مراقبة البيئة البحرية):يعد سبائك التيتانيوم ضروريًا للمكونات المغمورة لفترات طويلة، ويتم استكماله بسبائك PPO/PS والألمنيوم المؤكسد لتحسين التكلفة.وبطبيعة الحال، فإن ما ورد أعلاه هو إرشادات عامة.المبدأ الأساسي يظل كما هو:يمكننا تحقيق التوازن بين الأداء والتكلفة من خلال الجمع بين المواد الأساسية منخفضة التكلفة والأجزاء الأساسية عالية الأداء؛أو تعظيم كفاءة الأداء مقابل التكلفة من خلال التصاميم الهجينة (على سبيل المثال، تضمين التعزيزات المصنوعة من سبائك التيتانيوم في الإطارات البلاستيكية).
في المقالة التالية، سوف نستكشف المواد الناشئة عالية الأداء المناسبة للتطبيقات الأكثر تطلبًا.